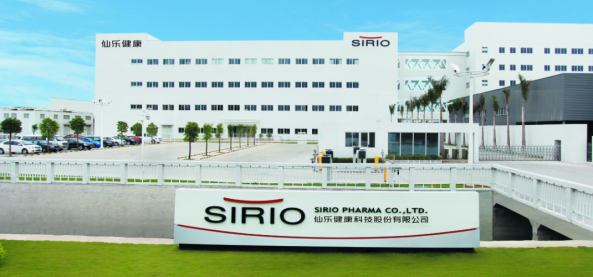
•亞洲最大軟膠囊生產(chǎn)基地
•中國(guó)第一家植物膠軟膠囊生產(chǎn)企業(yè)
•中國(guó)第一家保健品批量出口企業(yè)
•中國(guó)最大的的營(yíng)養(yǎng)保健品合同生產(chǎn)商
•連續(xù)6年業(yè)績(jī)?cè)鲩L(zhǎng)超過(guò)30%
•連續(xù)6年中國(guó)保健品出口排名第一
•與多家世界500強(qiáng)企業(yè)的成功合作經(jīng)驗(yàn)
•兩大生產(chǎn)基地,多種業(yè)務(wù)合作模式
[明確導(dǎo)入范圍以及目標(biāo)]
一、APS項(xiàng)目實(shí)施目標(biāo):
(1)提升PMC效率,滿足客戶交貨期
(2)實(shí)現(xiàn)集成供應(yīng)鏈:按需生產(chǎn)、按需交付材料,提高訂單物料齊套率,降低庫(kù)存
二、APS導(dǎo)入范圍:分四個(gè)階段
第一階段:主生產(chǎn)計(jì)劃(MPS)
基于包裝工序拉動(dòng)前制造半成品生產(chǎn),降低半成品庫(kù)存,提升訂單達(dá)成率,平衡各生產(chǎn)線產(chǎn)能,合理調(diào)配包裝線人員,實(shí)現(xiàn)準(zhǔn)確ATP。
第二階段:物料交付計(jì)劃
基于前制造,包裝主計(jì)劃拉動(dòng)物料進(jìn)料計(jì)劃,實(shí)現(xiàn)按需進(jìn)料,降低材料庫(kù)存,提高齊套率
第三階段:物料齊套/欠料分析
基于實(shí)時(shí)庫(kù)存與進(jìn)料計(jì)劃分析原料、包材的欠料、訂單的齊套情況,快速而精確的掌握計(jì)劃安排的準(zhǔn)確性,確保計(jì)劃的可執(zhí)行性
第四階段:詳細(xì)生產(chǎn)排程(DPS)
基于確定的主生產(chǎn)計(jì)劃展開各工序的車間執(zhí)行計(jì)劃,確保車間各工序有序安排生產(chǎn)。

[導(dǎo)入實(shí)施的經(jīng)過(guò)]
APS導(dǎo)入實(shí)施從2016年11月到2017年7月30,項(xiàng)目組歷經(jīng)近8個(gè)月時(shí)間全部成功上線,由供應(yīng)鏈計(jì)劃部牽頭,集團(tuán)IT部全力協(xié)助,計(jì)劃部、IT部核心人員長(zhǎng)期投入,全職人力約17人,涉及銷售、商務(wù)、計(jì)劃、采購(gòu)、生產(chǎn)、工藝、物料、倉(cāng)庫(kù)以等各部門人員兼職參與。
[項(xiàng)目實(shí)施成果]
一、流程革新成果
(1)采購(gòu)生產(chǎn)銷售協(xié)同模式變革
APS項(xiàng)目的運(yùn)行使用,引入了MPS主計(jì)劃,高級(jí)物料交付計(jì)劃的概念,建立了基于MPS-物料交付的采購(gòu)、生產(chǎn)、銷售的協(xié)同模式,克服了傳統(tǒng)采購(gòu)、生產(chǎn)、銷售會(huì)事前分析太少、數(shù)據(jù)不規(guī)范、可視化程度差等弱點(diǎn),增強(qiáng)了數(shù)據(jù)分析能力、快速?zèng)Q策能力,使得采購(gòu)、生產(chǎn)、銷售協(xié)同,數(shù)據(jù)系統(tǒng)化、實(shí)時(shí)化。
(2)計(jì)劃模式的變革
導(dǎo)入APS系統(tǒng)前前制造計(jì)劃,包裝計(jì)劃獨(dú)立排產(chǎn)沒(méi)有關(guān)聯(lián)性,各自為主體,前制造不能快速依據(jù)包裝計(jì)劃的變化而變化,造成前制造半成品庫(kù)存增加。物料采購(gòu)按傳統(tǒng)的ERP 接訂單通過(guò)無(wú)限能力產(chǎn)生采購(gòu)需求,不能真正的按排產(chǎn)計(jì)劃拉動(dòng)物料需求,通過(guò)APS的實(shí)施計(jì)劃模式由包裝計(jì)劃為中心,拉動(dòng)前制造計(jì)劃,克服了前后計(jì)劃間不能密切聯(lián)系的困境,優(yōu)化了以傳統(tǒng)MRP計(jì)算材料進(jìn)料的模式,采用按APS 排產(chǎn)計(jì)劃計(jì)算物料需求,進(jìn)行材料采購(gòu)的高級(jí)物料計(jì)劃模式,從以前每天進(jìn)行計(jì)算物料計(jì)劃,到一周兩次集中計(jì)算物料計(jì)劃的轉(zhuǎn)變。
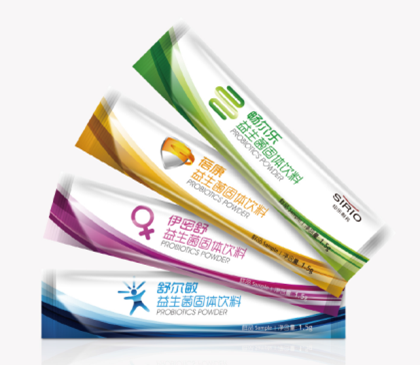
(3)欠料齊套分析變革
APS欠料齊套分析的使用,改變了之前在ERP 中按下的采購(gòu)訂單、庫(kù)存,查要排的訂單是否有料,人工查詢時(shí)間長(zhǎng),不清楚物料被拿些計(jì)劃使用的情況,采用APS欠料齊套分析可精確的基于實(shí)時(shí)庫(kù)存,供應(yīng)商承諾的到料時(shí)間對(duì)所有排產(chǎn)計(jì)劃進(jìn)行統(tǒng)一的欠料&齊套分析,準(zhǔn)確掌握物料被用在那些訂單上,特別是對(duì)共用料的把握更準(zhǔn)確,及時(shí)把握計(jì)劃的可執(zhí)行性,也提高了交期答復(fù)的準(zhǔn)確性及時(shí)性。
(4)計(jì)劃指令系統(tǒng)化下達(dá)
APS排產(chǎn)后自動(dòng)生成生產(chǎn)批號(hào),將計(jì)劃任務(wù)下達(dá)到ERP,取消了傳統(tǒng)的手工定批號(hào),下任務(wù)的模式,實(shí)現(xiàn)了CRM-APS-ERP數(shù)據(jù)的實(shí)時(shí)共享。為生產(chǎn)計(jì)劃系統(tǒng)化、可視化、透明化管理搭建了平臺(tái),并起到了關(guān)鍵作用。
導(dǎo)入效果
(1)計(jì)劃管理系統(tǒng)化+數(shù)據(jù)驅(qū)動(dòng)管理模式變革
APS系統(tǒng)實(shí)現(xiàn)了從人工排產(chǎn)到系統(tǒng)排產(chǎn)再到自動(dòng)排產(chǎn)的跨越。從最初人工排產(chǎn)時(shí)交集少、協(xié)同差,到現(xiàn)在前后工序系統(tǒng)排產(chǎn)一體化,聯(lián)動(dòng)性加強(qiáng),不斷提高著排產(chǎn)的準(zhǔn)確性,加強(qiáng)了快速的應(yīng)對(duì)變化的能力,實(shí)現(xiàn)了計(jì)劃管理模式的跨越式發(fā)展,整體管理水平從經(jīng)驗(yàn)管理邁向數(shù)據(jù)驅(qū)動(dòng)管理。
(2)計(jì)劃協(xié)同,應(yīng)對(duì)變化效率大幅提高
APS系統(tǒng)上線之前,計(jì)劃排產(chǎn)模式為前制造半成品計(jì)劃,包裝產(chǎn)品計(jì)劃各自獨(dú)立排產(chǎn),訂單變化,需要通過(guò),郵件、電話確認(rèn)、手工模擬協(xié)調(diào)、以及前制造設(shè)備多資源協(xié)調(diào)逐個(gè)計(jì)劃調(diào)整,耗費(fèi)一天時(shí)間,系統(tǒng)上線后,在以包裝為中心拉動(dòng)前制造計(jì)劃的模式下,當(dāng)訂單發(fā)生變化,包裝重新自動(dòng)排產(chǎn)后,前制造可以自動(dòng)更新計(jì)劃快速進(jìn)行模擬由系統(tǒng)自動(dòng)分派資源,重新制定新的計(jì)劃,效率提升60%左右。
(3)實(shí)績(jī)報(bào)工統(tǒng)一管理、計(jì)劃制定更加精準(zhǔn),計(jì)劃達(dá)成率提升
規(guī)范實(shí)績(jī)收集的業(yè)務(wù)操作,強(qiáng)化實(shí)績(jī)收集的準(zhǔn)確、及時(shí), APS根據(jù)最新、最及時(shí)的實(shí)績(jī)快速制定未來(lái)有效的計(jì)劃,提升了計(jì)劃執(zhí)行的達(dá)成率,達(dá)成率在系統(tǒng)導(dǎo)入前由80%提升到95%左右
(4)計(jì)劃下達(dá)規(guī)范化程度提升,建立生產(chǎn)批號(hào),真正實(shí)現(xiàn)以計(jì)劃為中心拉動(dòng)整個(gè)生產(chǎn)運(yùn)作
建立以生產(chǎn)計(jì)劃為中心的計(jì)劃體系,由計(jì)劃下達(dá)生產(chǎn)批號(hào),以計(jì)劃批號(hào)為鏈條貫穿整個(gè)計(jì)劃執(zhí)行過(guò)程,使得下達(dá)執(zhí)行計(jì)劃規(guī)范,數(shù)據(jù)流向有依據(jù),有條理。
(5)物料采購(gòu)實(shí)現(xiàn)按需、有節(jié)奏的進(jìn)料,降低材料庫(kù)存
基于MPS主計(jì)劃計(jì)算物料需求,按照合理的進(jìn)料節(jié)奏,可以按日、周、旬、月等進(jìn)料方式進(jìn)行進(jìn)料,拉動(dòng)物料按需進(jìn)料、按需合理備料,在提升進(jìn)料達(dá)成率的同時(shí)也提升了訂單交付率,材料庫(kù)存也有所下降,APS導(dǎo)入后Q4同比上年原輔料下降約5%,包材類下降約6%