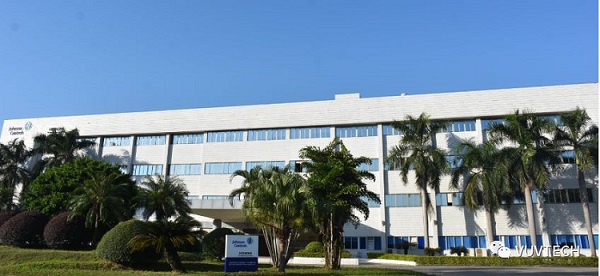
1.現(xiàn)狀:
生產(chǎn)計劃聯(lián)系緊密,產(chǎn)品量產(chǎn)品種多,試驗產(chǎn)品多;訂單變化快,幾乎每天都有計劃變更;物料種類多, 定轉(zhuǎn)子鐵芯,動定盤原材料生產(chǎn)廠家必須一致,導(dǎo)致物料計劃制定不能準確按需求進料,導(dǎo)致響應(yīng)變化效率低,交付能力弱,已經(jīng)成為業(yè)務(wù)發(fā)展的瓶頸,導(dǎo)入高級生產(chǎn)計劃系統(tǒng)迫在眉睫。因此需要更先進、更專業(yè)的排程系統(tǒng)。
2.業(yè)務(wù)特點:
1. B2B模式,基于訂單、預(yù)測生產(chǎn)模式,客戶多,產(chǎn)品型號多,更新?lián)Q代快,產(chǎn)品質(zhì)量追溯要求高,計劃變動頻繁
2.部件大部分自制,同時還有自制外發(fā)采購并存,計劃層次多
3.部件共通、型號多、批量小,換線多,部分原材料采購周期長
3.項目導(dǎo)入背景:
1. 多部件計劃聯(lián)動困難:從組立計劃到半成品多層計劃排產(chǎn),周期長,變動聯(lián)動困難
2. 合并生產(chǎn)減少切換難:客戶多,半成品多,多品種小批量合并生產(chǎn),順序優(yōu)化減少切換
3. 部件內(nèi)制外發(fā)并存:需要考慮內(nèi)制最大化
4. 生產(chǎn)計劃和物料計劃協(xié)同難:根據(jù)每層詳細生產(chǎn)計劃確定物料需求數(shù)量和時間點
[明確導(dǎo)入范圍以及目標]
一、APS項目實施目標:
(1)按需生產(chǎn)、按需交付材料,提高訂單響應(yīng)能力
(2)提升快速交付能力
(3)快速科學的進行物料和產(chǎn)能分析
(4)拉動供應(yīng)鏈物料JIT交付能力
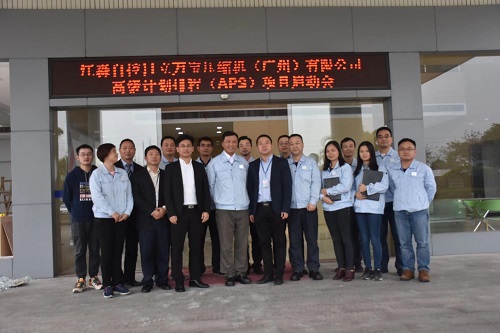
二、APS導(dǎo)入范圍:分三個階段
第一階段:組立計劃詳細排產(chǎn) 【組立計劃排產(chǎn)+物料齊套分析】
1.對營業(yè)給定的確定訂單進行正向排產(chǎn),并對滿足合批條件的訂單進行合批生產(chǎn)及優(yōu)化排產(chǎn)。
2.基于物料庫存,在途進行物料齊套分析,以判斷組立計劃的可執(zhí)行性,及時掌握物料欠料情況。
第二階段:各零件詳細生產(chǎn)排程
1.各零件詳細生產(chǎn)排程(DPS)
?基于確定的組立計劃展開各零件的車間執(zhí)行計劃,確保車間各工序有序安排生產(chǎn)。從上到下拉動式排產(chǎn),上下游互為承諾體系, PSI滿足
?下游計劃在考慮滿足上游需求同時,考慮合批,順序優(yōu)化減少切替損失
?與ERP集成,實現(xiàn)快速客戶需求獲取,快速ERP物料協(xié)同計劃安排
第三階段:CTB預(yù)測產(chǎn)能與齊套分析
根據(jù)營業(yè)提供的全年12月預(yù)測需求,計算出工廠的最大產(chǎn)能(不考慮人員,設(shè)備情況)。根據(jù)工廠所需物料的交付特點(交期前3個月可以波動50%,2個月波動30%,1個月波動10%)同步放大材料交付數(shù)量后計算出每天的齊套情況與欠料情況。
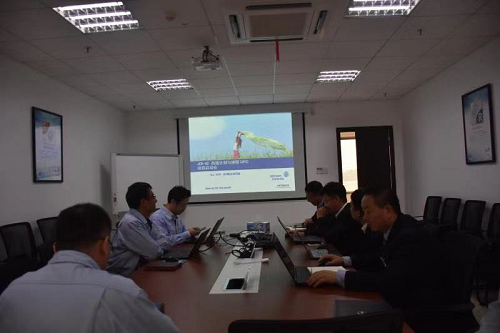
[導(dǎo)入實施的經(jīng)過]
排產(chǎn)易導(dǎo)入實施從2018年9月到2019年9月,項目組歷經(jīng)近一年的時間全部成功上線,由生產(chǎn)部門牽頭, IT部全力協(xié)助,計劃部、IT部核心人員,項目組核心成員長期全職投入,涉及銷售、計劃、采購、生產(chǎn)、工藝、物料、倉庫以等各部門人員兼職參與。
[項目實施成果]
(1)業(yè)務(wù)流程標準化
上系統(tǒng)之前所有的前置工作都堆積在生管(在U8系統(tǒng)中沒BOM,工藝產(chǎn)能是怎么樣的,在哪線生產(chǎn)合適),上系統(tǒng)后在源頭上進行了控制,沒有BOM,工藝產(chǎn)能信息的訂單不允許進行排產(chǎn),有效減少了返工時間。
(2)銷售端快速答復(fù)
大幅度的提高了計劃排產(chǎn)的效率。當日下達的銷售需求,當日排產(chǎn),當日進行ATP回復(fù);
(3)建立起采購,生產(chǎn),銷售一體化平臺
銷售與生產(chǎn)一體化:上系統(tǒng)之前銷售通過Email,電話等各渠道與生管進行訂單的管理。上系統(tǒng)后都在aps中進行,并且進行了條件約束,比如1.單筆訂單不能超過1000,以免造成占用過多產(chǎn)能;2.已轉(zhuǎn)U8工單審核后進行生產(chǎn)的訂單不能進行修改,以免造成數(shù)據(jù)混亂;3.生產(chǎn)計劃在7天內(nèi)的訂單需要主管進行修改等等。
生產(chǎn)與采購一體化:上系統(tǒng)之前生產(chǎn)需要與采購電話溝通材料情況,采購需要手工收集最新的材料需求,上系統(tǒng)之后擔當可以在aps中計算與查看所需的信息。
(4)U8生產(chǎn)訂單指令系統(tǒng)化下達
APS排產(chǎn)后自動,將所有工單計劃任務(wù)下達到U8,取消了傳統(tǒng)的手工下發(fā)模式,極大地提高了作業(yè)效率,實現(xiàn)了APS與U8,APS與MES數(shù)據(jù)的實時共享。為生產(chǎn)計劃系統(tǒng)化、可視化、透明化管理搭建了平臺,起到了一個指揮棒的作用。